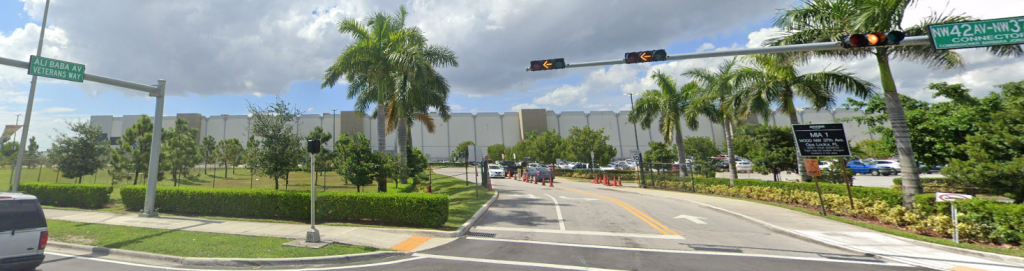
I took Amazon up on their offer to tour a fulfillment center yesterday. The visit was as much Amazon’s attempt at bluewashing as it was an opportunity to learn how the massive retailer handles logistics.
At 800,000 square feet, MIA1 is relatively small on Amazon’s scale (the smallest US fulfillment center is 600,000 sq ft, with the largest being over 3 million square feet), but the team is quite proud of their productivity — noting that they’ve shipped over 1,000,000 packages in a single day multiple times (with the achievement on Prime Day 2023 being immortalized on a banner near the entrance). Our tour leader even mentioned that MIA1 often outperforms larger facilities, like the one in Jacksonville and another near LaGuardia.
Here’s how the tour worked:
Arrival
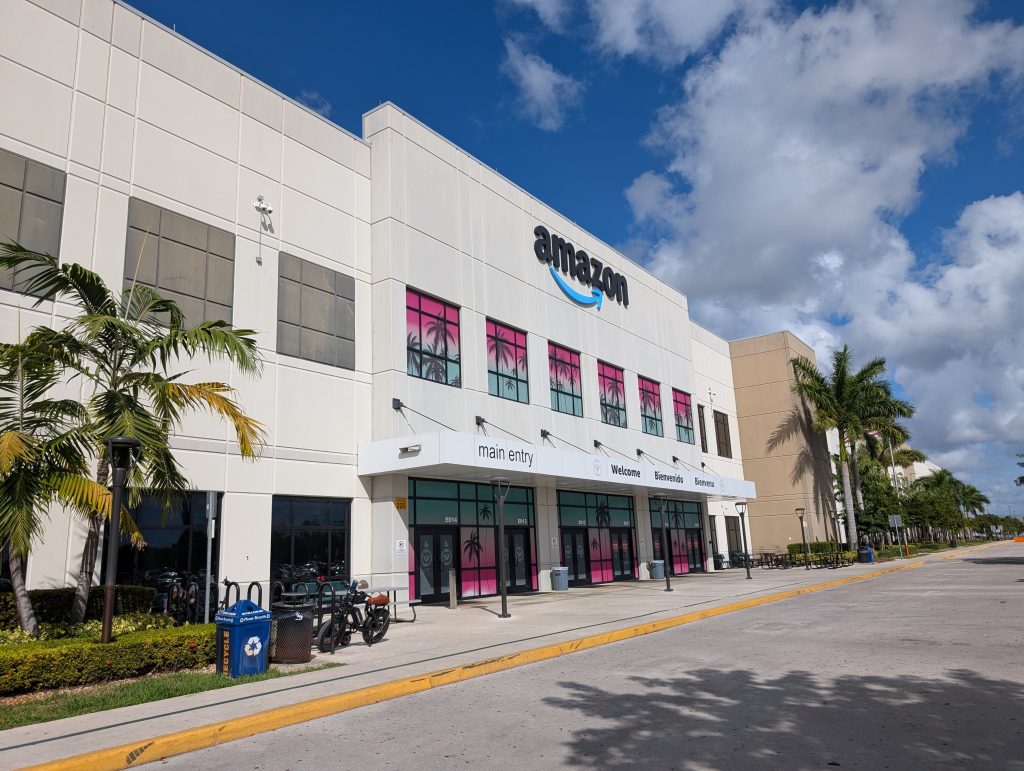
The parking lot is large and full. It was a decent walk to the entrance. As instructed, I arrived about 15 minutes prior to the start of the tour. The “waiting area” is the employee entrance. So we stood in air conditioning a few feet from the twelve massive turnstiles that allow Amazon employees to enter and exit. A trickle of employees coming and going was constant. Some even wore their IDs at just the right height (on their upper arm) so they could scan the sensor and pass through the entrance gate without breaking stride.
While I’ve been in my share of warehouses (my last corporate job was with a nine-figure retailer that coordinated all product coming/going through a single facility) and I did a project with UPS at Miami HQ near MIA during college, among others, this facility was loud. Once we got inside, there were frequent warnings/reminders to wear protective ear coverings.
At some point, a guard emerged — Wonka-like — through a simple metal door and checked ID’s against a printed out registration list.
As I waited I saw signs that indicated pictures would not be allowed. I expected this, but was disappointed.
Right on time we were led through the guard’s door and into a simple meeting room. Despite generating $628 billion in revenue in 2024, the meeting room was as plain and ordinary as any medium or large sized business — even for one in a warehouse. The tables and chairs were simple. A short welcome and safety video was played — and the video was larger than the screen it was projected onto. It was fine, but not perfect. Something of a theme of things to come. I don’t say that as a knock on Amazon or the fulfillment center. I say that as a reminder to all business people — myself most certainly included — that getting things 100% perfect isn’t always necessary.
This theme carried throughout the tour, where we saw many standing workstations for managers and supervisors. These had nice (usually HP) computer set ups with wired mice and keyboards. Everything was atop a simple wooden desk. These looked like something you’d slap together with pieces you pick up at Home Depot than something you’d order from a catalog. They weren’t fancy. They weren’t adjustable height. But they looked sturdy.
Our tour guide introduced himself and the rest of the tour team — four other folks would follow along to open doors and make sure none of us got lost (on purpose or accident) along the way. Our guide was super friendly and knowledgeable. He “joked” a few times about how everyone eats lunch standing up and managers eat with a laptop in one hand and food in the other.
The Tour
Here’s a 10 minute video that’s very similar to the tour I took. Rather than recap each step that’s outlined in the video, I will highlight things that stood out to me. (Apparently there were/are virtual tours too — this review includes some screenshots, including a deeper discussion of the robotics than was part of this tour).
After we were all given headsets (so that we could hear our guide), we started on the tour. First we were taken for safety shoe covers (which we wore over our regular shoes) and were walked past the display for Black History Month, the in house, branded merchandise area, HR, and a break area (which was outfitted with various tools and devices to help you stretch and work out muscle aches).
Our first official stop was the restroom. I checked it out as an old mentor advised me that a restroom gives you the quickest and best insight into how a company takes care of it’s facilities. MIA1’s were clean and unremarkable. I took this as a good sign.
A massive break room / lunch area was adjacent to the restroom area, but we didn’t get a chance to see it. As we walked back towards the HR area we stopped to see some massive televisions where our tour guide explained how any associate (employee) can ask a question and have it answered. Any topic is fair game and questions are answered in the language in which they are asked (we saw questions in English, Spanish, and Creole). Having just glimpsed the lunch room, a question about microwaves jumped out at me — someone asked whether microwaves could be designated for certain dietary restrictions and Amazon responded that they could. The break room now has microwaves only for vegan food, halal food, and others.
Large screens like these were a theme of what we would see throughout the tour. Some displayed current work assignments. Others answered HR questions. Others displayed KPIs for each department. There were also many areas that had large, rolling whiteboards with KPIs and important information on them (who was leaving early, who was new, etc) on them. Nothing was overly fancy. But massive amounts of information were being communicated clearly.
We stopped in the storing area of the 3rd floor to see how the storying and picking takes place. On the way there we walked through through a Hall of Fame for people who have picked 5,000+ items during a shift. Each person who has achieved the feat gets their picture taken with a robot. Their picture is labeled with a summary of their accomplishment and is framed in the hall. Two-thirds of the hallway is probably filled and the remaining third has frames waiting for pictures. This felt like a nice way to recognize people and to encourage everyone to keep striving.
The work area for arriving inventory, storage of inventory, picking, packing, and shipping of items was plain. But the work product was impressive. No one person is doing anything seemingly complicated. But they are working fast. A machine is constantly telling them what to do next. And they are being timed while they do it. The only way to stop the clock is to press a button or scan an item (depending on your task) which causes the next task to be given to you.
For associates storing and picking items, each workstation had at least two screens — one telling the associate what to do (put item X in Y) and another that gamified their work (a literal video game they were “playing” by doing their work where they were also being scored and ranked in a fun (seeming) and friendly (seeming) way).
During our tour there was an (undisclosed) issue in the storing and picking area. Workers finished what they were doing and were immediately reassigned to another area. This process was remarkably quick and efficient.
There is no “high value” area on the floor. High value goods are intermingled with ordinary and low value goods. The explanation of this was two-fold. One: it’s difficult to distinguish between ordinary value and high value goods on the floor (say earrings) and it all needs to get picked and packed quickly. Second: there’s a scan for all employees on the way out. Clear bags and the like are required. If you leave with more than you entered, you will be caught.
We visited a single item packing area (where your order would be packed if you ordered 1 item). Each workstation has 1 employee, a simple keypad, a few sensors, and pretty much every conceivable box you could receive from Amazon. The system tells the employee which box to pick based on the item purchased. The seller pre-selects which box you receive (and is apparently to blame if your box is too small or large). Based on the box, the system automatically dispenses the correct amount of tape for the bottom and top of the box, which the person simply applies.
The SLAM area was unmanned, but equally fascinating. Items that had issues were automatically kicked out and sent to a Problem Solver (another kind of associate). Most packages continued on their way to be routed to a truck and eventually make their wy to your home.
SLAM stands for Scan, Label, Apply, and Manifest. This entire process was fascinating.
The Robots
While we didn’t get much detail on how the robots work (“no one touches them… you need special training to go into that area… they run on an algorithm”), they were amazing to watch. Each weighs about 300 pounds and can lift up to 2,500 pounds. They glide gracefully around the “closet” area between the storers and pickers without colliding. We were told the robots charge themselves when their battery falls below 15%.
There were a handful of robot shells hung from the ceiling near the facility entrance. These were signed by folks who had worked with the robots since the facility opened in 2018.
Safety Culture
While some of this was Amazon making sure to tell those of us on the tour how focused on safety they are, the fulfillment center is clearly focused on safety.
The floor is clearly marked. Tape notes where it is safe to walk, where work is happening, and where things can be stored. At workstations the footprint for garbage cans is clearly and precisely marked.
Throughout the floor there are Grainger vending machines that dispense personal protective equipment. Everything is dispensed through your ID, meaning that each employee is entitled to a certain amount of equipment based on their role. It appeared that additional equipment could be purchased through payroll deduction.
Each employee receives a $110 credit to Zappos to buy work shoes (steel toed shoes).
There are safety stations along the floor with soap, paper towels, bandages, and the like. These tables also hold 3 electrolyte dispensers (think Gatorade mix) that you can squirt into your water bottle to make a flavorful drink. The tour leaders were quick to point this out — and also to emphasize that Amazon added touchless water dispensers during the pandemic so that workers could stay hydrated, and all because Amazon cares about their associates so much.
Priorities
In addition to safety, Leadership Priorities are on display throughout the facility. While I couldn’t take pictures, Amazon’s Leadership Priorities are well documented online. Customer Obsession, Ownership, Invent and Simplify, and Hire and Develop The Best are displayed prominently near employee break areas.
Near workstations three are prominently displayed:
- Keep your area clean and organized
- Be present in your area, constantly engage / coach associates
- Obsess over day-over-day improvements
The focus on day-over-day improvements really jumped out at me. I know a lot of businesses and leaders that focus on year-over-year, month-over-month, week-over-week, and performance versus budget/forecast. But the day-over-day focus in Amazon’s fulfillment centers is great and makes a lot of sense. We all remember yesterday. We were a part of it. There’s no argument about who set the budget or what external factors affected last month or last year. It’s about being better than yesterday. Simple as that.
Stats and Facts
- A minimum of 2,000 people are working at MIA1 at any given time. Up to 6,000 work at peak times
- People primarily work in one of 2 10-hour shifts. The facility is running 24/7 because of folks working part time, donut shifts, and the like
- Items begin being packed and shipped within 20 minutes of you placing your order (which also explains why it can be difficult to cancel an order that you ‘just’ placed)
Other thoughts
While MIA1 isn’t too far from me, on my drive I realized that I was closer to at least 2 Amazon fulfillment centers. That alone tells you something of the size and scale of Amazon’s operation.
MIA1 is located next to Miami’s Opa Locka airport. The facilities are separated by only a small two lane street. While not discussed during the tour, being near an airport, but without the traffic of nearby MIA or FLL has obvious benefits.